ピッキングの改善が難しい理由
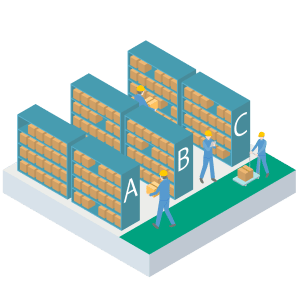
ピッキングといえば物流センターや倉庫における作業の中で多くの方がお悩みをかかえるものではないでしょうか。
物流現場には他にも入出荷、入出庫、流通加工などいくつかの作業がありますが、なぜピッキングが度々そのように課題上がってしまうのでしょうか。
今回はその背景をご紹介します。
その1:人手不足
物流は全ての業界と比較してもとりわけ人材が不足している業界です。
下のグラフは各業界の2021年1月から2022年9月までの人手不足の度合を示したものです。
日本銀行が四半期に一度公開している統計の短観より作成しました。
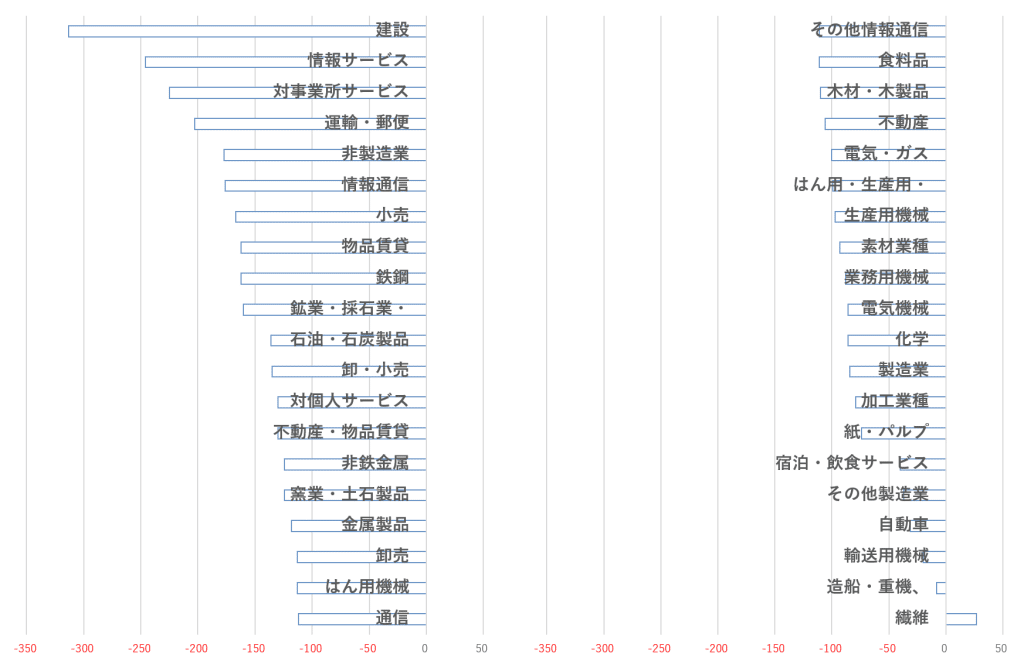
全体的にマイナスなのですがその中でも物流業界に関わる対事業所サービス業が下から3番目に位置し、運輸・郵便業が続いています。
(対事業所サービス業とは、「「事業所」からの収入が事業収入額の3分の2以上を占める業種」を指し、倉庫業、修理業などが当て嵌まります。)
また、日本全体の労働人口の減少や、ECの規模拡大により人手不足は今後も継続して深刻化していきます。
ピッキングのような構内作業は基本的に人手で行うものですからその影響を強く受けます。
その2:組み合わせ爆発
人手が足りないのであれば、 作業を効率化させるほかありません。
ピッキングとはあらかじめ渡されたリストや注文書をもとに指定の品物を集め、まとめたものを検品担当者や梱包担当者へと受け流していく業務です。
ピッキングではある地点からある地点へ人が移動を繰り返します。
ですからその順番を考えることでピッキングを効率化できる可能性があります。
では、その組み合わせはどういった増加推移を辿るかご存知でしょうか。
実際に図で確認してみましょう。
例えば2か所なら最初にどちらを選ぶかだけなので2通りですね。3か所だと6通りになります。そこまでの増加幅でもない様に思います。
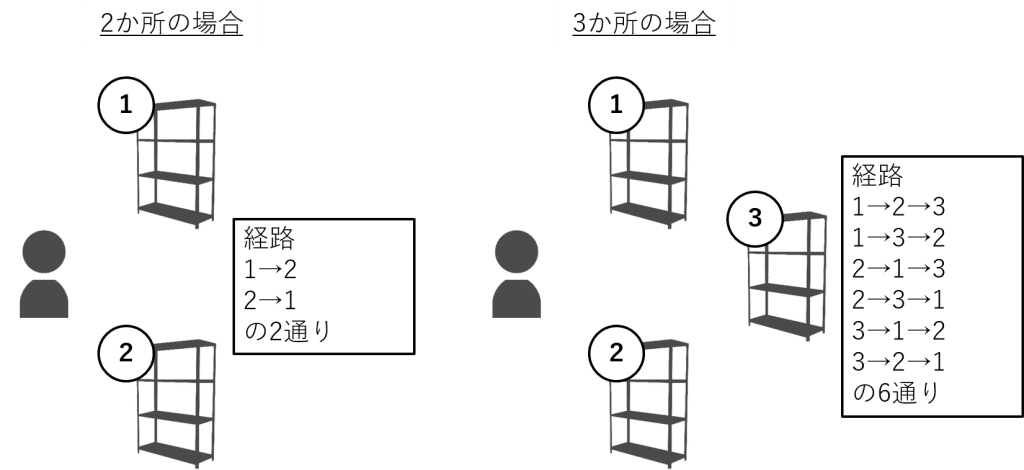
実はこれは階乗で増加していきます。
階乗というのはN!で表される、N以下のすべての自然数を掛け合わせた数値です。(自然数とは0を除く正の整数です)
となると、
4か所(4!)は4*3*2*1=24か所
5か所(5!)は4!に5を掛けるので120か所
と、地点が一つ増えるごとに急激に増加するようになり
10か所(10!)では約360万(3,628,800)通り
20か所(20!)では約240京(2,432,902,008,176,640,000)通り
100か所(100!)ともなると0が68も続く無量大数さえも突破します。
このように組み合わせを検討する際はNの数が増えるにつれ今回の階乗や指数関数によって急激に複雑化してしまいます。これを組み合わせ爆発と呼びます。
ピッキングといえば毎日、何種類ものオーダーが発行されます。それが10か所で百万を超えてしまうような代物なのですから効率化も単純な話ではありません。
その3:様々な効率化
このように人員の不足とそもそもの複雑さからピッキングが課題になることが分かりました。
勿論、これだけ厄介なお話ですからそれに対する解決策は無数にあります。
例えばロボットやマテハン機器を導入し作業を自動化してしまうことです。
こうすれば人手不足の問題は勿論、効率性も問題もある程度度外視できるようになります。規模に応じて様々なソリューションが用意されています。
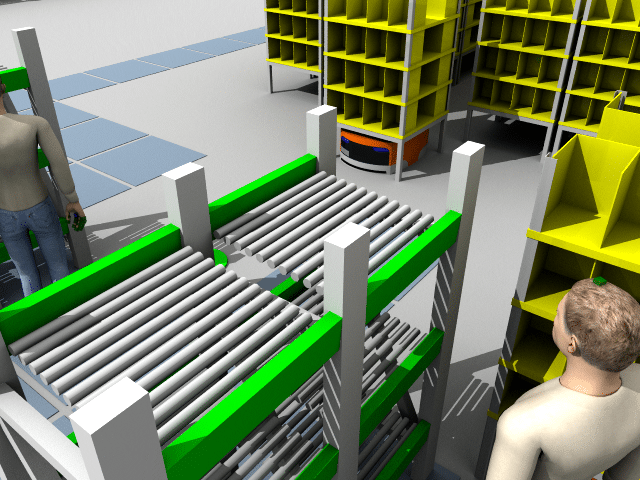
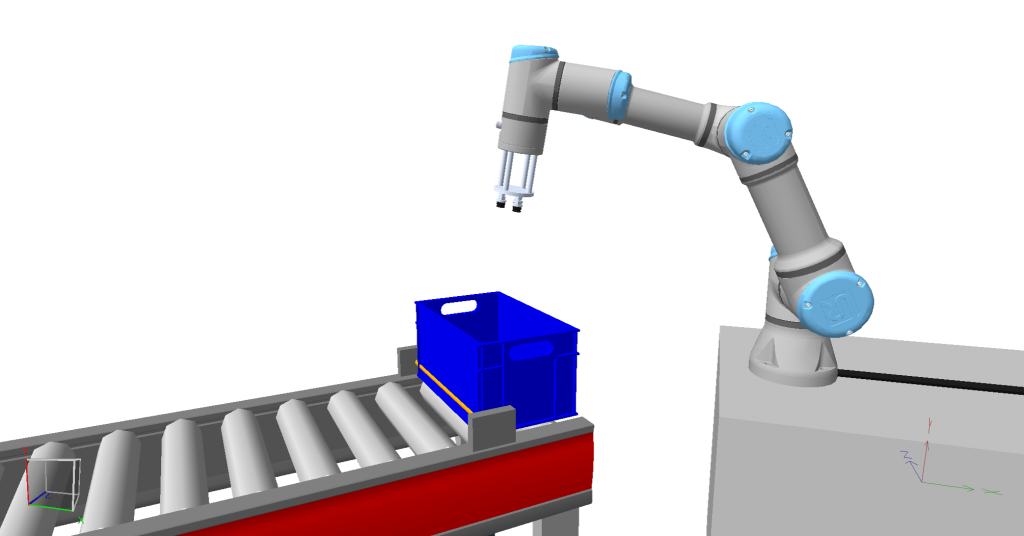
ロボットを使ったピッキングの効率化についてまとめた記事はこちら
GAS DPS AGV…ピッキングを効率化するソリューションをまとめてご紹介します
またはソフトウェアを使って課題解決する方法もあります。
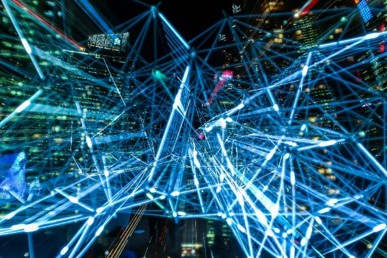
量子コンピュータを使えば、理論上、組み合わせ爆発を起こす計算を一瞬で完了できます。
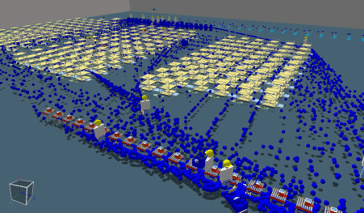
シミュレータやAIを使い近似解(比較的良い値)を算出する方法も効果的です。
ただ、これらはいずれも数百万から数千万と莫大な費用が掛かります。
もちろんそれらはその値段相応の機能を備えていますが、非常に多様なソリューションがあるがゆえになかなか最適な選択が難しくもあります。
安価に即座にピッキングを改善
ピッキングの改善が難しい理由ご理解いただけましたでしょうか。
皆様の業務に少しでもお役立ていただければ幸いです。
弊社でもピッキングの改善ツールを販売しております。
高価で多機能なソリューションが様々ある中、弊社製品「ロジアナ君」はピッキングに特化し、安価に即座にピッキングを改善できるソフトウェアとなっております。
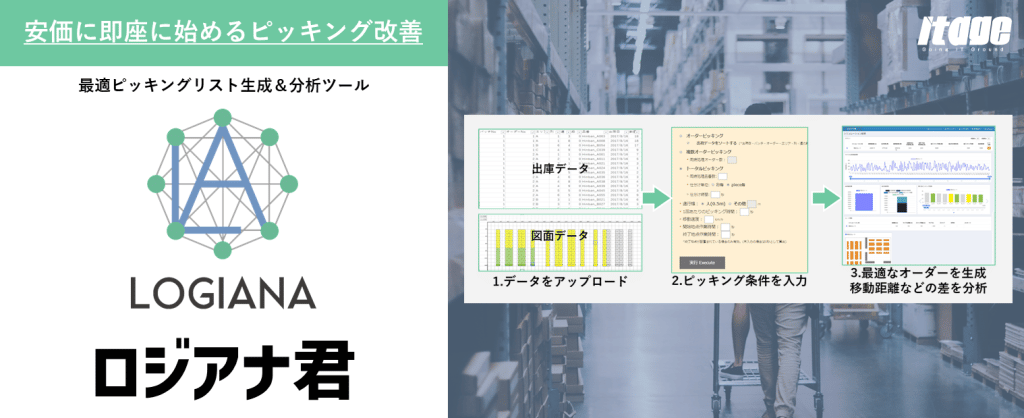
ピッキングに課題をお抱えの方は是非一度ご確認ください。