ピッキングとは?物流倉庫の業務効率化を目指す
皆さまこんにちは、株式会社ITAGEの中元です。
今回は、物流センターにおける「ピッキング」についてご紹介します。
ピッキングとは?
皆さまは、「ピッキング」と聞いてどんな場面を思い浮かべますか?
特殊な工具を用いて玄関のドアを開錠する場面…
ドラマや映画で1度は目にしたことがあるのではないでしょうか。
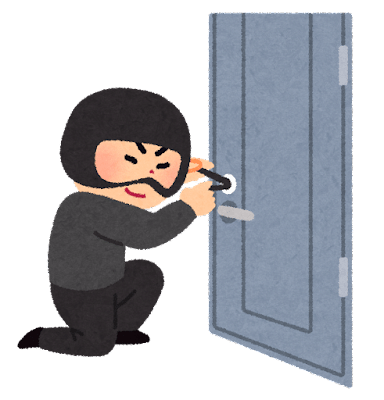
今回ご紹介させていただく「ピッキング」はこれとは全く異なります。
では、どんなものかと言いますと…
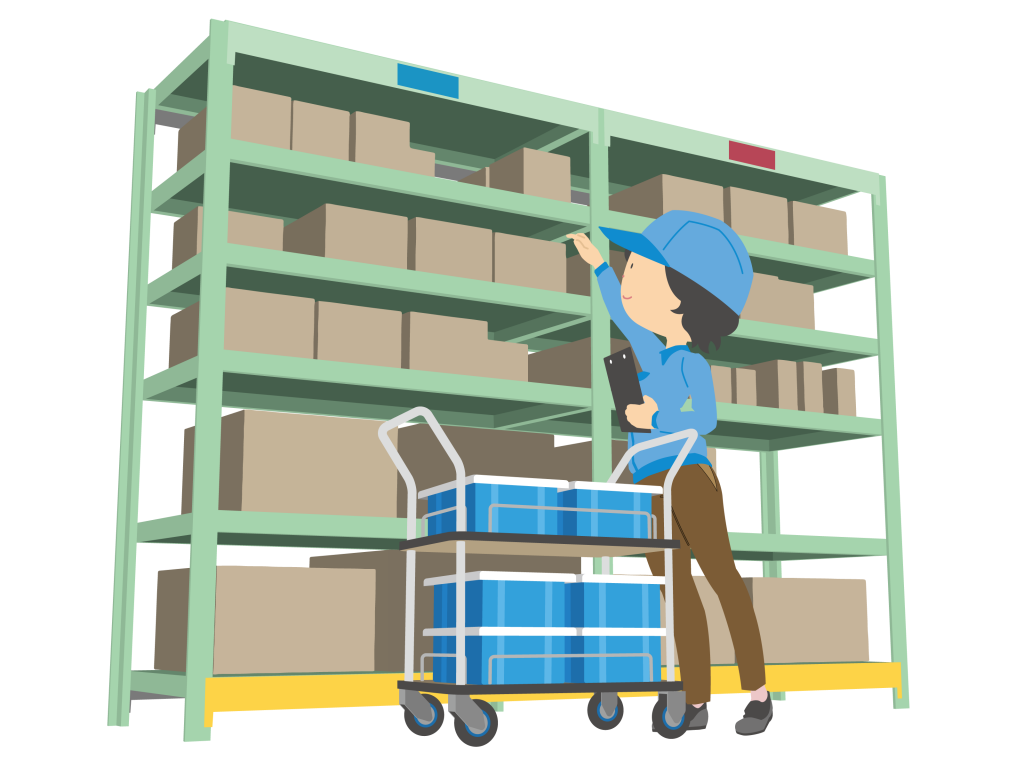
このような物流センターや工場倉庫内における「ピッキング」です。
今回はこちらについてご紹介させていただきます。
物流センターにおけるピッキング
伝票や指示書(ピッキングリスト)に基づいて、商品を取り出す作業のことです。
ピッキングの目的は、指示書に書かれた品番や数量通りに商品を集め、梱包や検品といった次工程にまとめて供給することです。
必要な商品を、少ない労力・コストで確実に集める(ピックする)ことが重要です。
仕分けとの違い
似たような言葉として「仕分け」があります。
こちらは、商品を出荷先別・品種別など、目的に応じて分類していく作業のことです。
両者は似たような意味として使用される場合もありますが、違いを明記すると、次のようになります。
・ピッキング:(保管されている商品を)取り出す。
・仕分け:(入ってきた商品を)分類、区分けする。
基本的には
仕分け ➡ 保管 ➡ ピッキング
という流れですが、ピッキングの種類によってはピッキングの後に再度仕分け作業が必要です。
ピッキングの種類
ピッキングには大きく分けて2つの種類があります。
① オーダ式ピッキング方式(摘み取り方式)
商品を集める際に出荷先(オーダ)ごとに集める方式の事で、最も一般的な手法です。
急な注文があった場合でもすぐにピッキング作業に入ることができるなど、柔軟性が高いことが特徴です。しかしながら、出荷先の数だけ倉庫内を歩き回ることになるため 、品種の重なりが大きいと作業効率が低下します。出荷先や品種が多い場合は移動時間や商品の場所を探す効率が課題となり、作業者が倉庫内から商品を探しやすくなるような工夫が必要です。
② 品種別ピッキング方式(種まき方式)
全ての出荷先(オーダ)を一括してピッキングする方式です。
複数の出荷先を一括でピッキングするため、オーダ別ピッキング方式と比較して倉庫内の移動を最小化することが可能です。商品を探しに倉庫内を何度も回るということは無く、作業員の移動負担は減少しますが、後工程で出荷先別に仕分けを行うことが必要です。
つまり、オーダ式ピッキング方式(摘み取り方式)の場合は
仕分け ➡ 保管 ➡ ピッキング
という流れですが、品種別ピッキング方式(種まき方式)の場合は
仕分け ➡ 保管 ➡ ピッキング ➡ 仕分け
という流れになります。
どちらの方式がより効率が良いのかは、条件や目的によって異なります。
自社倉庫にどのピッキング方式を採用するのかといった判断は、とても難しいものです。
しかし、ピッキングを含めた出庫工程は最も時間やコストがかかる過程であり、
出庫の方式の良し悪しが物流センターの評価を分けると言っても過言ではありません。
ピッキングを効率化することは、倉庫内業務改善において重要なポイントであると言えます。
最後に
いかがでしたでしょうか。
今回は、物流センターにおけるピッキングについてご紹介いたしました。
先ほども申し上げたように、ピッキングは倉庫業務の改善において重要なポイントです。
しかし、どのように改善を始めたら良いのか分からないという方も多いのではないでしょうか。
そのような、ピッキングの効率化についてお悩みの方に、弊社の「Emulate3D」をお勧めします!
ピッキングをシミュレーションし、最適なピッキング導線を検討することが出来ます。
簡単なレイアウト変更により、大幅な効率改善につながる場合もございます。
ピッキング作業で改善できる部分がないか、ご検討してみてはいかがでしょうか。
今回ご紹介したEmulate3Dの詳細はこちらをご覧ください。